Isomer Monitor MDI/TDI
MDI-Based Solutions for Global Manufacturing Needs
MDI (Methylene diphenyl diisocyanate) is an essential component in manufacturing high-performance products worldwide, from thermoplastics and flexible foam to automotive parts, adhesives, coatings, elastomers, and footwear. MDI exists in three distinct isomers—2,2′-MDI, 2,4′-MDI, and 4,4′-MDI—that react with polyols to form polyurethane, a material prized for its durability and versatility.
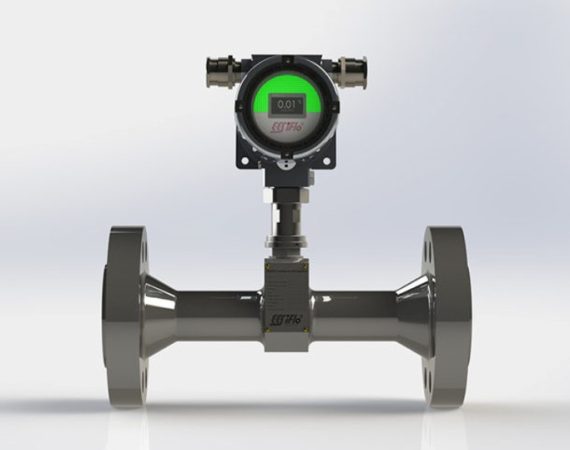
Major chemical companies, including Dow Chemical and BASF, are prominent MDI producers and part of the Isocyanate Institute, which emphasizes safety in MDI and TDI (Toluene diisocyanate) production and usage environments.
To support safe and efficient processes, EESIFLO has engineered an advanced solution for real-time identification of polymer variations in MDI by measuring the dielectric constant. Developed in collaboration with industry leaders, this reliable technology has been successfully implemented and operational across various industrial sites for several years. This solution exemplifies EESIFLO’s commitment to innovative products that meet stringent industry requirements for both safety and performance.
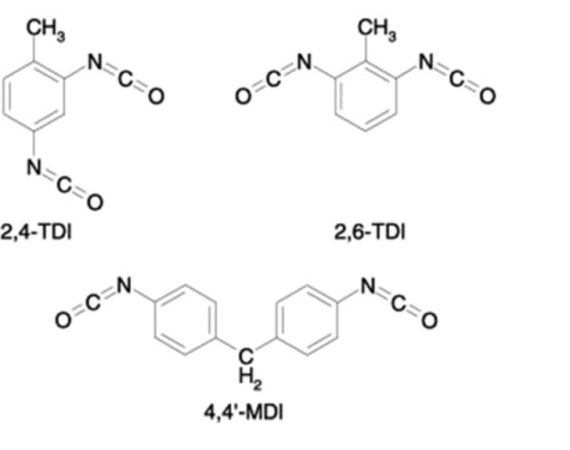
Background on EESIFLO's MDI Monitoring Development
In the late 1950s, scientific advancements revealed that measuring the dielectric constant of fluids with high accuracy was possible in laboratory settings. This finding paved the way for developing tools that could identify different isomers of MDI (Methylene diphenyl diisocyanate) in real time. Recognizing the potential for online, real-time monitoring, EESIFLO embarked on creating an efficient solution to address this need.
Historically, online fluid measurement relied on chromatographs, which, while accurate, are often costly and inefficient for continuous monitoring. EESIFLO’s innovative MDI monitor uses dielectric constant measurement to distinguish fluid types accurately and economically. Rigorous EMC third-party testing has validated the device for safe use in hazardous locations, such as Zone 1 areas.
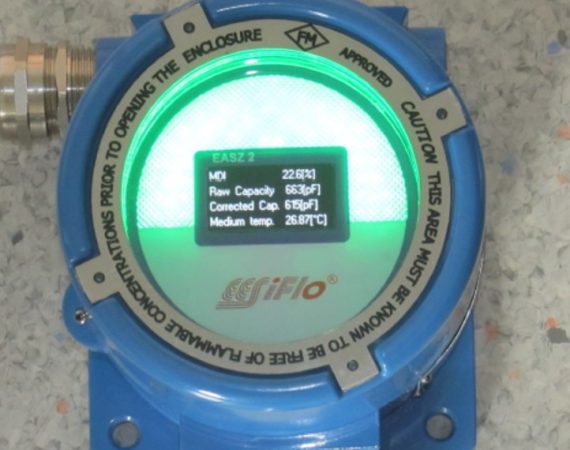
EESIFLO’s cost-effective solution enables online monitoring at multiple points without high costs, helping avoid the limitations of manual sampling or costly delays. The device is ideally suited for chemical industry applications, such as MDI and TDI (Toluene diisocyanate) processing, supporting process engineers in both modernizing and automating new facilities or retrofitting existing ones.
For U.S.-based companies seeking custom solutions, EESIFLO offers tailored dielectric-based sensors for MDI and TDI applications, backed by extensive industry expertise and responsive customer support.
PRODUCT
Do You Simply Need a Monitoring System?
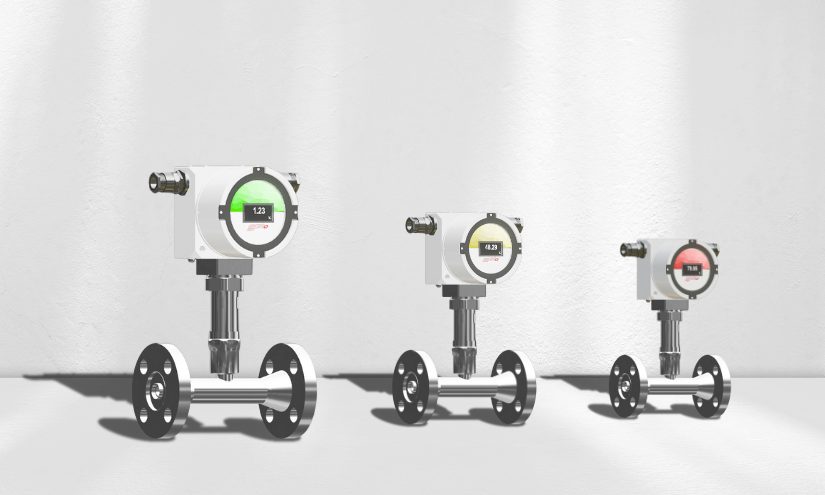
Additional points of consideration:
- A typical process controlling dynamic crystallisation. Instead of time and temperature controlling your process, you can actually see the MDI molecular content changing in real-time. This saves time and so more batches can be produced per 24 hours and can reduce hand/spot sampling and product wastage.
- A typical process controlling static crystallisation. You will be able to fine tune the output of your crystalliser in real-time. This will help you to produce “first time right” products and again, it saves time doing hand/spot sampling and product wastage.
- Monitoring your downstream processes in real-time. Knowing the MDI concentration at any point in the process to make sure your process is fully optimized.
- TDI concentrations can also be identified by dielectric constant measurements so the same MDI units can be used in TDI processes.
- An added feature is the ability to detect water too. If a user is concerned about water entering the MDI or TDI system? The EESIFLO MDI monitoring instrument can function as early warning system to even shutdown your processes if this occurs.
Technical Specifications
24VDC power supply and comes with: mA output, serial interface (Modbus)
- OLED display with colour warnings for high and high/high. Green in normal condition, amber and red for critical conditions.
- Open collector for alarm
- Measuring data is available as an MDI or TDI displayed output or dielectric constant. Temperature compensation
- Certified to a maximum process temperature of 90°C
- Empty pipe detection.
- Ex approval: ATEX II2GD / ATEX II3G EEx d / EEx de FM/CSA Cl. I Div. 1
- Application: Currently liquids only
- Nominal diameters 1” to 6”
- Process connections Flanges: DIN, ANSI, JIS Tri-Clamp®, VCO DIN 11851, DIN 11864, SMS 1145, ISO 285
- Process pressure Maximum 100 bar
- Wetted parts 316 L stainless steel
- Degree of protection IP 67
- Accuracy: Typically +/- 0.05%
Call +1 (318) 614-3971
Once the application is specified, the units can programmed to meet individual needs.