Flow Tests - Enhance Pump Testing and Diagnostics
For pump manufacturers, suppliers, and end users, verifying that pump specifications align with desired performance is crucial to maintaining operational efficiency and equipment longevity. Our non-intrusive flow meters offer an effective solution for obtaining precise flow data during pump performance tests, enabling users to ensure their system is meeting both design expectations and mechanical integrity standards. With the ability to monitor pump output in real-time, these flow meters help detect any deviations or declines in performance, facilitating timely maintenance decisions and adjustments before any significant issues arise. Whether
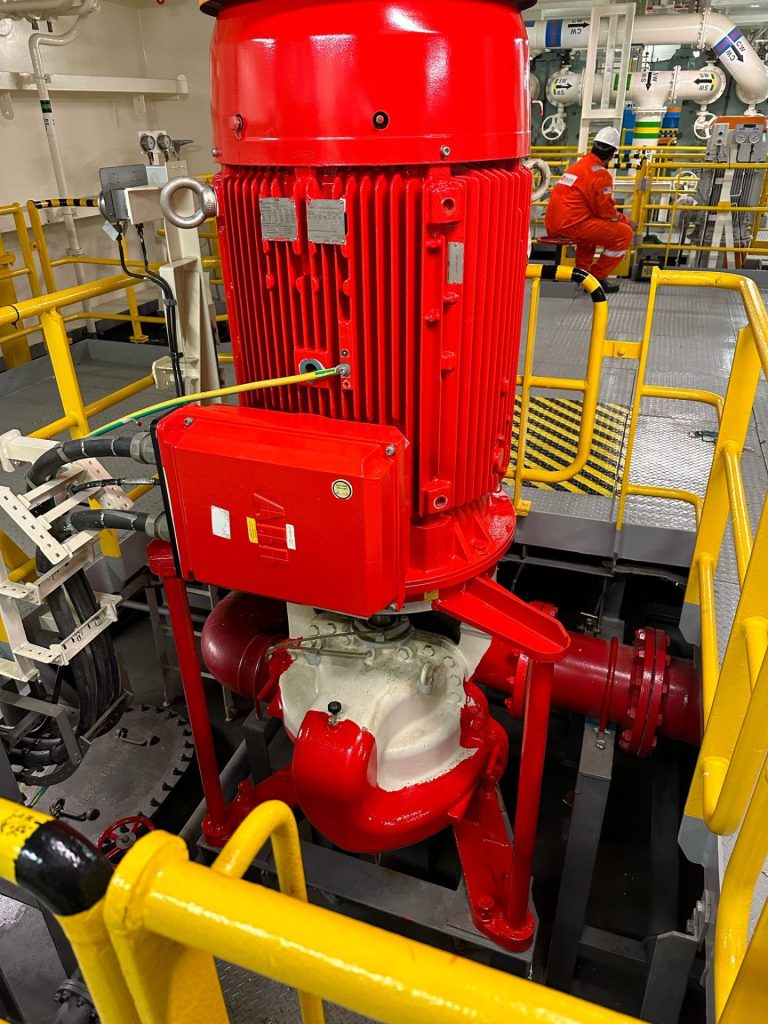
it’s a new installation or routine diagnostics, our flow meters provide the reliable data you need to make informed, proactive decisions for optimal pump operation.
Diagnosing Performance Declines
If a pump—especially a centrifugal one—has shown a decline in output (flow rate) after years of reliable service, it might be time for maintenance. Before modifying any mechanical components, a clamp-on flow meter can be used to assess the current output. Accurate flow rate data helps you make informed decisions about necessary repairs, such as replacing impellers or checking for wear.
Performance Curve Validation
When a new pump is delivered, it’s expected to follow a specific performance curve based on factors like RPM, head efficiency, horsepower, and Net Positive Suction Head (NPSH). While RPM can indicate flow rate, it doesn’t guarantee accuracy. A non-invasive flow meter offers a precise flow measurement, helping verify performance across various operational points without disrupting the system.
Ensuring System Integrity
Monitoring a pump’s integrity includes checking for optimal bearing temperatures, acceptable vibration levels, and absence of leaks from seals, gaskets, or o-rings. With our flow meters attached to the pipe, flow rates can be observed in real-time while technicians evaluate temperature and other mechanical factors, ensuring the pump operates smoothly under normal conditions.
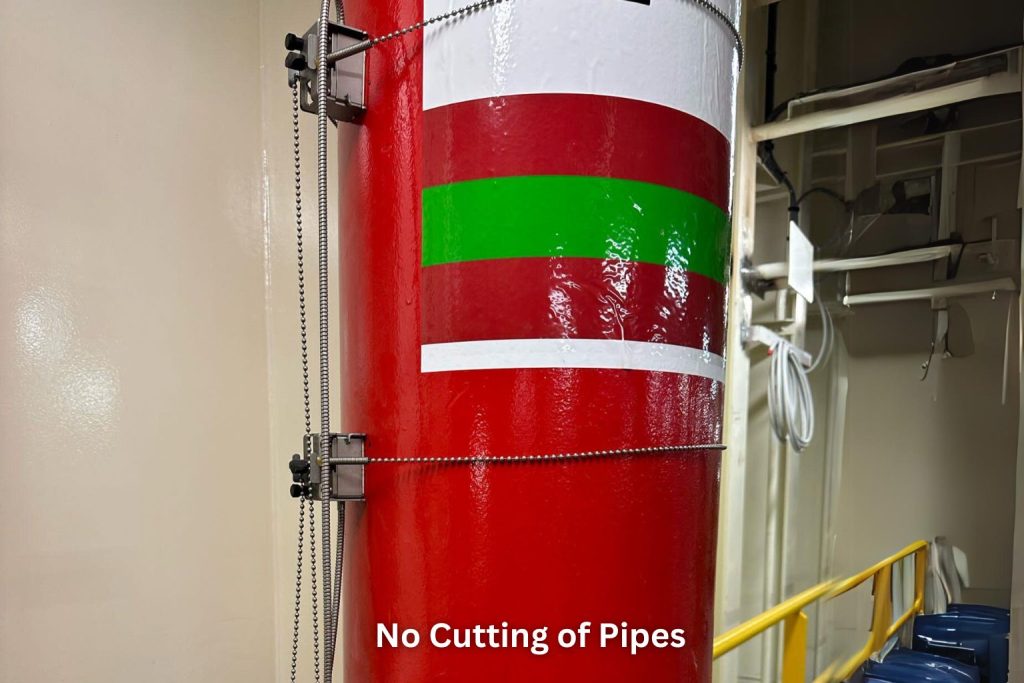
Enhancing Suction and Cavitation Checks
A pump’s suction capability and cavitation resistance can be tested more easily with a non-intrusive flow meter, especially when using a Variable Frequency Drive (VFD) for varied speeds. Our cross-correlation flow meters offer accurate readings across all flow rates, providing reliable data for both low and high-flow conditions.
Piping Insights
Pump issues aren’t always internal—sometimes, the problem lies with the piping itself. Using our flow meters, technicians can read flow velocities at multiple points along the pipeline. By analyzing flow data at each section, it’s possible to pinpoint where piping issues might be affecting the pump’s performance, leading to quicker and more efficient troubleshooting.
Adaptability to Various Liquids
One of the standout advantages of our flow meters is their adaptability to different liquid types. From water to oils and chemicals with varying densities and viscosities, our tools deliver accurate measurements regardless of the fluid’s properties. This versatility means that your flow meter can be reliably used across diverse pumping applications.
PRODUCT
Rent or Purchase Flexibility
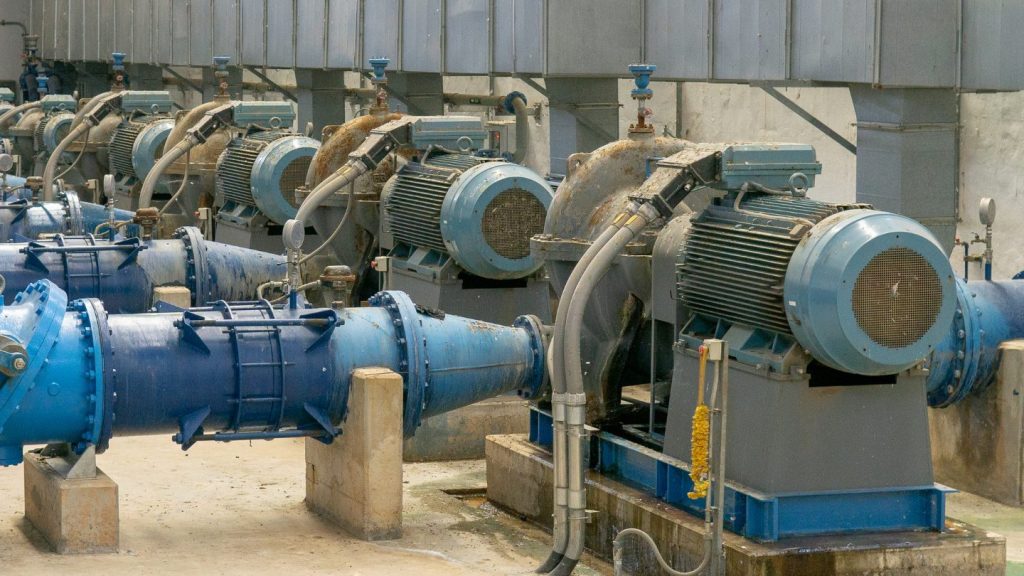
Renting to Own
If you’re uncertain about long-term needs, we offer flexible options to rent or rent-to-own our flow meters. Test the performance and reliability firsthand, and when you’re ready, choose to buy or upgrade as needed.
Call +1 (318) 614-3971
Our non-intrusive flow meters are trusted by technicians for precise and repeatable readings, allowing for streamlined pump testing, diagnostics, and maintenance. With EESIFLO, accurate flow measurements are at your fingertips, supporting optimal pump performance in a variety of industrial applications.